What are the advantages of contracting CESSI Ergonomics Consulting Specialists? – SOLUTION RESULTS!
Is an ergonomic process worth the costs – YES! Not only is ergonomics good for your people, it is good for the bottom line of your business. It doesn’t matter whether your company is big or small, nor does it matter what type of industry you are in. While our solutions may vary, our approach does not – effective and sustainable results!
CESSI’s comprehensive services, strategies and customized solutions work! Healthy employees are your company’s most valuable asset which results in enhanced performance within your organization. Implementing ergonomic processes are an effective way of supporting your investment in people. Each CESSI professional possesses the knowledge and expertise to help you achieve the ergonomic results you need and expect.
Poor ergonomic practices result in workers who are fatigued, experience discomfort issues, are physically challenged and are not able to perform their job to the best of their ability. These symptoms can lead to employees’ absenteeism, loss of productivity, recurring job turnover and ultimately injuries. Indirect costs associated with an employee’s work leave can be many times greater than the direct cost of an injury.
Good ergonomic practices impact the health, safety and success of your workforce. Implementing an ergonomic process throughout the company results in comfortable and supportive work environments which provide increased health benefits. Workers’ concentration levels, quality work output and employee morale are significantly improved. Making these changes reduces physical work demands, lowers injury rates and decreases workers’ compensation costs. In most cases, work efficiency and productivity results increase as well.
Productivity Results Case Study
Cosmetics Industry
Order Entry & Fulfillment Department
The Challenge
CESSI conducted an ergonomic case study for a client in the cosmetics industry to determine possible productivity gains in their order entry and fulfillment department. First, the company’s management decided to have a departmental audit conducted to determine workplace challenges and to create an order entry rate as a control standard.
Each order entry clerk would receive orders coming in from their sales representatives and input the products and shipment information into the system so the orders could be fulfilled and shipped out to the customers. The department was able to capture the number of keystrokes electronically, determine the number of keystrokes each agent typed per minute and how long it took them to completely process an order. The study began by looking at the data shown below.
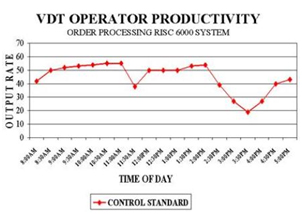
The cosmetic company’s order results indicated that right before lunch the numbers of orders processed dropped. After the lunch break the number of orders slowly increased until mid-day. Then the number of orders processed decreased significantly until their work break around 3:30 pm. The increase in productivity after the work break was not nearly as high as after their lunch break. Fatigue and order entry errors were identified as causes of the large drop in order out-put. How could they improve these order entry numbers, they asked?
The Solution
CESSI recommended a height adjustable desk and a fully adjustable ergonomic chair for each order entry clerk. Once the workers were comfortable using their new equipment, their keystrokes were measured again (data shown below). The entire productivity curve went up but they still had drop off periods throughout the same time periods every day. The afternoon drop off had improved.
After the ergonomic equipment was installed, the order entry productivity gain in the afternoons was 11.9% higher than before.

Progress, right? But, what else could they do to improve these numbers? CESSI provided an Ergonomics 101 training seminar to the order entry associates to teach them what ergonomics was, how it relates to them, how to use their ergonomic equipment correctly, and how working in healthy postures would benefit them throughout the day. Once the order entry team learned about ergonomics and went back to work for several days to incorporate their new working postures and habits, the study was then continued. Their entry keystrokes and orders processed were reassessed. The associates reported improved energy during the day and had fewer order errors which resulted in a raised out-put curve.
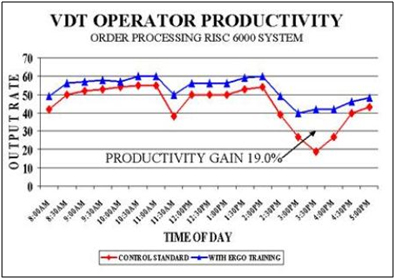
The Results
The final study results show that the entire productivity curve increased to a higher level which meant the order entry associates were keying at a faster rate and more orders were being processed during each 30 minute interval. Due to the fact that the overall productivity curve increased throughout the day, the drop offs were not as significant before lunch or before afternoon breaks as they were initially. The cosmetic company could clearly determine that productivity was increased after ergonomic equipment was installed but was at its highest rate after ergonomic training was included.
The most significant part of the study was that there was a 19% gain in productivity in the afternoons after ergonomic equipment was installed and ergonomic training had been completed.